Process Costing 101: How to Allocate Costs in Manufacturing
A comprehensive guide to understanding process costing and methods for allocating costs in manufacturing operations.
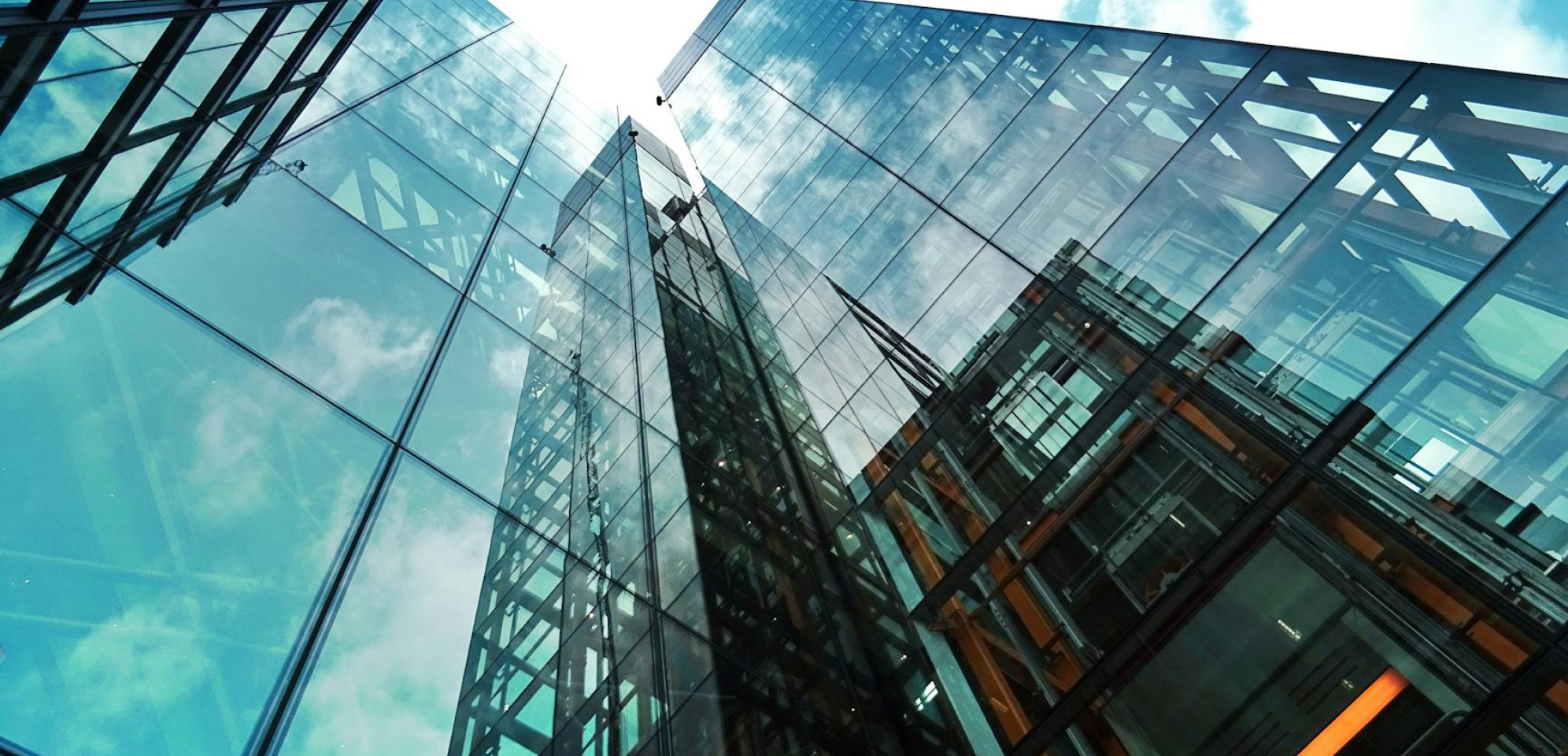
Understanding your production costs can make or break your manufacturing business. We see it all the time working with companies that make large quantities of similar items. Whether you produce plastic bottles, cell phone cases, or frozen dinners, you need a solid handle on the costs flowing through your production lines.
That's where process costing comes in. We’ll walk you through how it works so you can start using it to manage costs in your high-volume manufacturing operation. With some simple steps to allocate expenses and track workflow, process costing gives you crucial insights:
- See your real costs for producing each item.
- Identify which processes are the most expensive.
- Value your work-in-progress inventory accurately.
- Make smarter decisions on pricing and production levels.
Implementing process costing takes effort, but it’s one of the most impactful things you can do to control costs. Read on to learn how to use this method to boost efficiency.
What is Process Costing?
Forget the accounting jargon — process costing is just a straightforward method to figure out what it actually costs to produce each of your identical, mass-manufactured items.
- Accumulating Costs: Direct costs like materials and labor, as well as indirect manufacturing overhead costs, are accumulated for each process or production department over a specific period (usually a month).
- Equivalent Units: The total costs are divided by the equivalent completed units produced during that period to calculate the cost per equivalent unit. Equivalent units account for partially completed work-in-process inventory.
- Cost Assignment: The equivalent unit cost is then assigned to the completed units transferred out of the process and the remaining work-in-process inventory.
- Continuous Flow Production: Process costing is suitable for industries with continuous mass production of homogeneous products like chemicals, food, beverages, plastics, etc., where units are indistinguishable from each other.
Process costing hence helps you allocate all those expenses across the units you produce in a period. You add up the total costs for each step in the process, like molding and packaging. Then you divide that total by how many units you completed in those steps.
Process Costing Visualization Example
A general example to visualize process costing from raw material to finished goods and COGS:
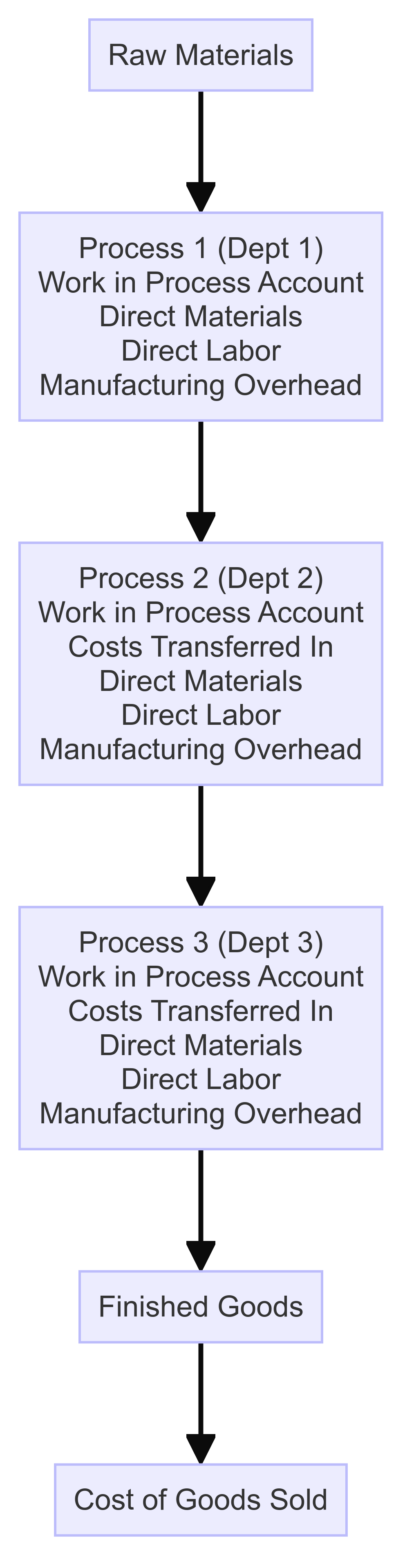
The flow diagram illustrates the following key steps in process costing:
- Raw materials are issued to the first production process or department.
- Costs such as direct materials, direct labour and manufacturing overheads are accumulated in the work in process account for each process/department.
- When a process is completed, the costs are transferred to the next process as "costs transferred in".
- This cycle continues through all production processes, accumulating costs in each department's work in process account.
- After the final process, the finished units are transferred to the finished goods inventory account.
- When the finished goods are sold, their cost is transferred to the Cost of Goods Sold account.
When Should Process Costing Be Used?
Let us illustrate some real-world reasons why process costing is a preferred method for high-volume manufacturers:
- Products are manufactured in large, homogeneous batches.
- Costs must be accurately tracked for inventory valuation and cost of goods sold.
- Managers need to monitor and control costs across production processes.
- Small cost changes can significantly impact profitability with high production volumes.
In essence, process costing is ideal for companies engaged in high-volume, continuous production of standardized products. It lets you see your real costs, value inventory accurately, and make smart operational decisions.
Process Costing in Action
Let's look at some examples of industries that rely on process costing:
- Oil refining: Oil refineries use process costing to assign costs to various steps like distillation, cracking, reforming and treatment. This determines the cost per barrel of refined products like gasoline, diesel and heating oil.
- Food processing: Process costing tracks costs across multiple stages like mixing, cooking, canning and labeling involved in mass production of canned foods or beverages.
- Chemical processing: Costs are analyzed across various steps such as reaction, crystallization, separation and purification for bulk production of chemicals.
- Pharmaceuticals: For drugs produced in large batches, process costing helps allocate costs to processes like fermentation, isolation, formulation and packaging.
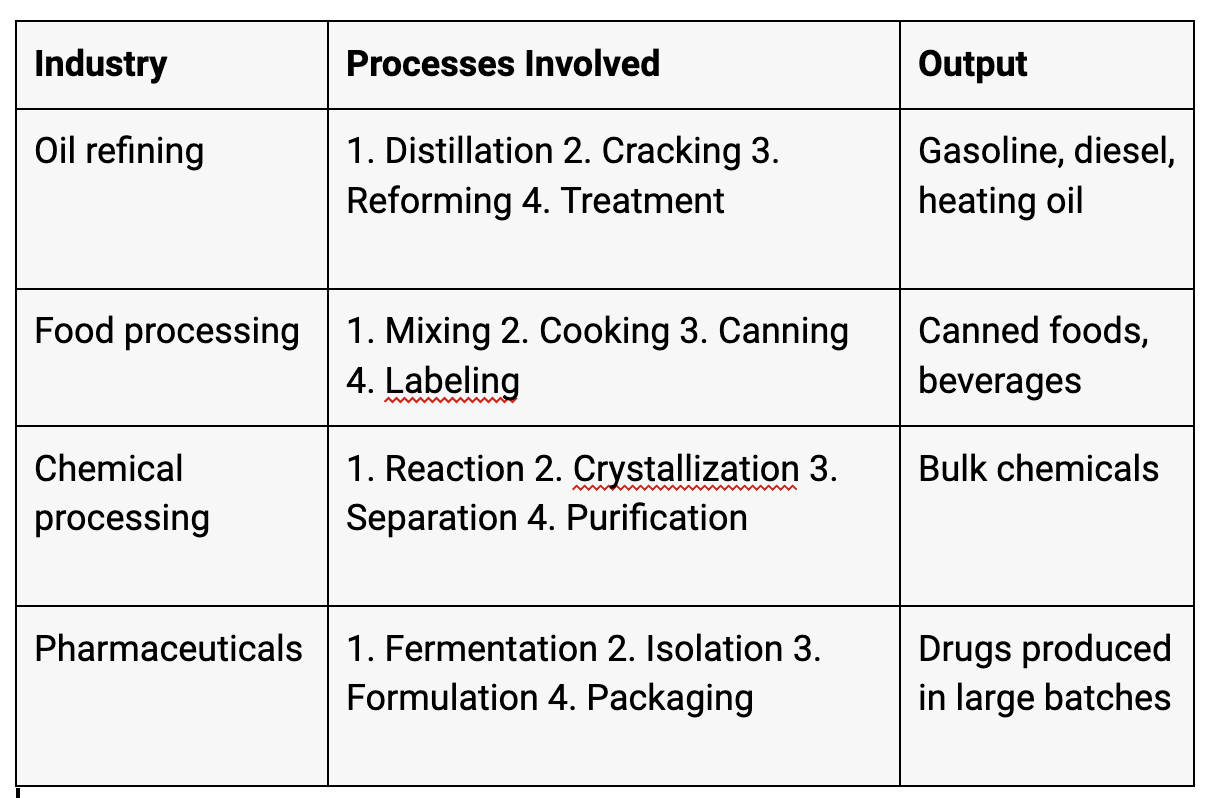
In each case, process costing provides vital data to value inventory, determine pricing and evaluate profit margins — for businesses producing identical goods at high volumes, it's essential.
Key Steps in Process Costing
Implementing process costing isn't too complex — it typically follows these 5 key steps:
- Summarize the flow of physical units: Track the number of units at each stage of the process — those begun, completed, and still in process.
- Compute output in equivalent units: Convert partially completed units into equivalent finished units based on their stage of completion.
- Summarize total costs for the period: Accumulate all costs related to each process - materials, labor and overhead.
- Calculate equivalent unit costs: Divide total costs by the equivalent units to get per unit costs.
- Assign costs to completed units and work-in-process inventory: Allocate the costs to fully finished and partially completed units.
That's the foundation in a nutshell. Now let’s walk through a detailed example to show how this looks in the real world. You'll see how a manufacturer would use these steps to get an accurate handle on their costs.
Steps for Process Costing with Examples
Let's break down the key steps involved in process costing using a practical example.
Consider a toy manufacturing company that uses plastic injection molding to produce homogeneous batches of action figures.
Each figure undergoes molding, painting, and packaging. In June, 60,000 units were started in the molding department. Here is how process costing would work
- Summarize Unit Flow
Beginning WIP (work-in-progress) inventor: 10,000 units
- Molding: 4,000 units
- Painting: 3,000 units
- Packaging: 3,000 units
Units started in molding during June: 60,000 units
Total units to account for: 70,000 units
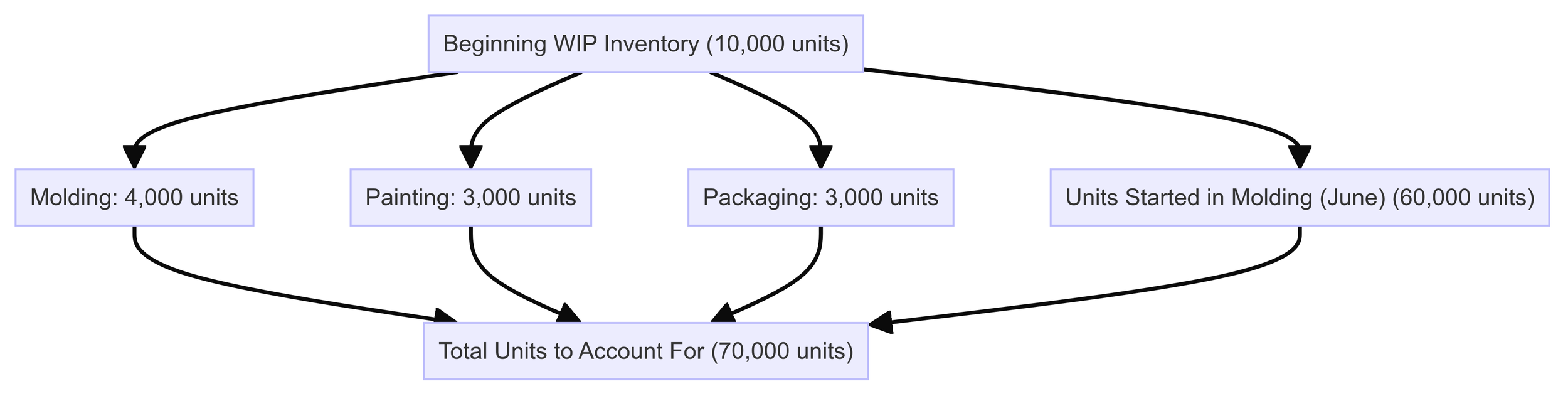
2. Calculate Equivalent Units
Units completed and transferred out from molding: 54,000 units
Units still in process:
- Molding: 4,000 units, 100% complete as to materials, 50% complete as to conversion costs
- Painting: 9,000 units, 100% complete as to materials, 20% complete as to conversion costs
- Packaging: 3,000 units, 100% complete as to materials, 0% complete as to conversion costs
Equivalent units:
- Materials: 70,000 units
- Conversion costs: 54,000 + 2,000 + 1,800 + 0 = 57,800 units

3. Summarize Total Costs
Total costs incurred in the molding department for June:
- Direct materials: $210,000
- Direct labor: $68,000
- Manufacturing overhead: $91,000
4. Calculate Equivalent Unit Costs
- Direct materials: $210,000 / 70,000 units = $3 per unit
- Conversion costs: $159,000 / 57,800 units = $2.75 per unit
5. Assign Costs to Units
Cost of completed units transferred to painting:
- Materials: 54,000 units x $3 = $162,000
- Conversion costs: 54,000 units x $2.75 = $148,500
Cost of ending WIP inventory:
- 4,000 units in molding, 100% complete for materials and 50% complete for conversion costs
- Materials: 4,000 units x $3 = $12,000
- Conversion costs: 4,000 units x 50% x $2.75 = $5,500
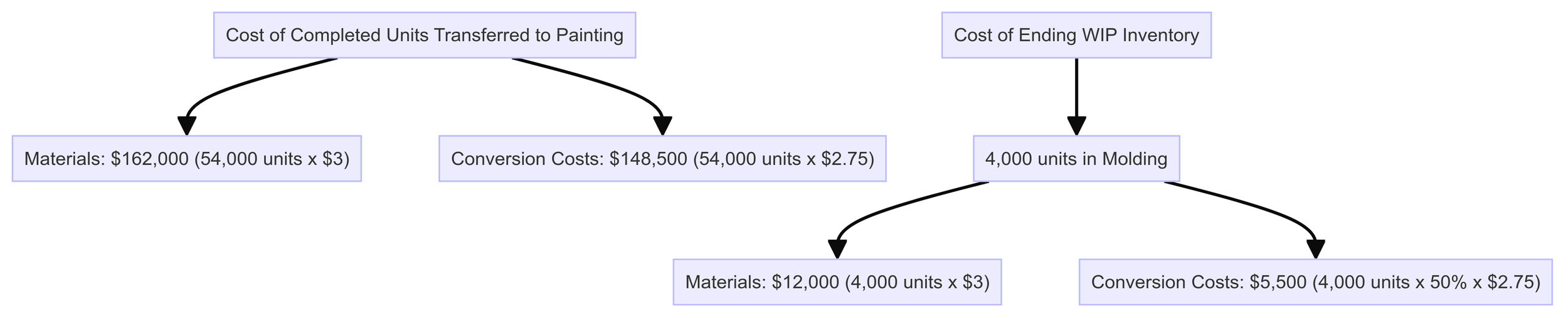
This example illustrates how process costing helps accurately allocate costs to units completed and to those still in production. The same method would then follow for the painting and packaging processes.
Benefits of Process Costing
Now that we've explored the steps involved, here's what advantages process costing brings to the table for high-volume manufacturers:
- Simplifies costing for homogeneous outputs: Process costing is easier to implement than job costing when producing standardized, identical products in batches.
- Enables accurate valuation of inventory: Process costing allows companies to accurately assign costs to units completed and units still in production for proper inventory valuation.
- Identifies costly processes and improvement opportunities: Analyzing costs by each production process highlights inefficient or problematic areas needing improvement.
- Supports pricing decisions based on production costs: Knowing the cost per unit from process costing provides the data needed for making informed pricing decisions.
- Helps determine profitability by product and process: Companies can use process costing to calculate profit margins by product line and by production process.
- Provides useful metrics for performance monitoring: Process costing offers production volumes, cost per unit, and other metrics to track performance over time.
- Adapts well to changes in processes or volumes: The process costing system can be adjusted if production processes or volumes fluctuate significantly.
- Facilitates effective cost control across departments: Accumulating costs by process allows focused cost control initiatives in high-cost areas or departments.
For companies engaged in high-volume production, process costing is simpler to implement than job costing. Implementing it takes effort, but it can supercharge your profitability and efficiency long-term.
Limitations and Challenges
However, process costing also comes with some limitations and challenges to watch:
- Assigns average costs rather than actual costs: Using an average cost per unit may not reflect variability in actual costs across units.
- Significant variation in production may make costs less accurate: Large fluctuations in production volume can reduce the accuracy of costs assigned per unit.
- Dependent on high-volume, consistent production for reliability: Process costing works best with stable, high-volume output and may be less reliable with inconsistent volumes.
- Provides less detailed cost information compared to job costing: Process costing gives average costs per department vs. job costing which traces costs to specific jobs.
- Allocating overhead costs can be complex with multiple processes: Determining appropriate overhead allocation rates for many departments can be challenging.
- Changes in processes or flow rates may require system adjustments: Shifting production processes or volumes may necessitate updates to the costing system.
Performing process costing manually can also be time-consuming and prone to errors. Using ERP or accounting software can help overcome some of these challenges.
Best Practices for Process Costing
To maximize the value derived from process costing, here are some best practices to follow:
- Clearly define each process or department for cost accumulation
Properly defining discrete processes and departments provides a framework to capture costs. For example, a furniture maker may define staining, assembly, and finishing as separate processes for accumulating direct materials, labor, and overhead costs. Clear process definitions are key for accurate data.
2. Develop procedures to capture costs accurately and consistently
Consistent procedures for gathering costs are vital for reliability. Standard forms, data collection workflows, and accounting guidelines help ensure costs are fully and accurately compiled each period. This data becomes useless if collection methods keep changing.
3. Calculate equivalent units systematically accounting for partial completions
Partially completed units must be converted to equivalent full units using a consistent, logical approach. For example, units 60% finished could be counted as 0.6 equivalent units. These equivalents should be calculated the same way each period, with documentation for review. Systematic equivalent unit calculations are critical for comparing costs across periods.
4. Use proper cost allocation bases for overhead costs
Not all overhead costs may relate directly to units produced. Appropriate cost drivers should be used such as machine hours, labor hours, or material quantities. For example, electricity costs could be allocated based on machine hours used in that process. The key is choosing allocation bases that accurately reflect how overhead resources are consumed.
5. Analyze significant variances in costs or production
Abnormal swings in cost or production data should be investigated. For example, a 20% increase in raw material costs per unit may indicate spoilage problems. Production bottlenecks may be signaled by a 10% decrease in units completed. Digging into unusual variances often uncovers important issues.
6. Review costing procedures periodically for needed adjustments
As production processes change over time, the costing system may need realignment. Performing periodic reviews ensures methods still provide accurate costs despite changes in production volume, flow, technology etc. This helps keep the system aligned to operational realities.
7. Leverage software tools to automate data collection and analysis
Collecting and processing data manually can be arduous and prone to error. Using accounting or ERP software with process costing features improves efficiency and accuracy. Automated analysis like cost variance alerts also enhances insights.
8. Compare costs over time and against benchmarks to identify improvement opportunities
Historical data and industry benchmarks provide context to identify issues and opportunities. For example, analyzing monthly trends could reveal a growing cost gap due to inefficient equipment. Comparing to benchmarks can highlight processes with above-average costs to target improvement initiatives.
While process costing has limitations, following best practices can help companies overcome challenges and use them effectively to manage production costs.
Conclusion
High-volume manufacturers face intense pressure to maximize efficiency. For producers of homogeneous goods, process costing is hence an invaluable tool to gain control of costs. By allocating expenses to each stage of production, it provides crucial data to value inventory, analyze profitability, and make strategic decisions.
Yet the benefits don’t come easily. Implementing process costing takes planning and diligence to accurately capture costs. That’s why leading manufacturers rely on specialized solutions like Unit IQ, which gives you deeper and more actionable insights about your unit economics. Our system automates data collection and analysis, providing real-time visibility into per unit costs, contribution margin, channel profitability, COGS, and more.
With process costing powered by Unit IQ, you can optimize production costs, adapt quickly to market changes, and drive profitability across your lines. Learn how industry leaders get end-to-end visibility today and request a demo.
Our latest posts
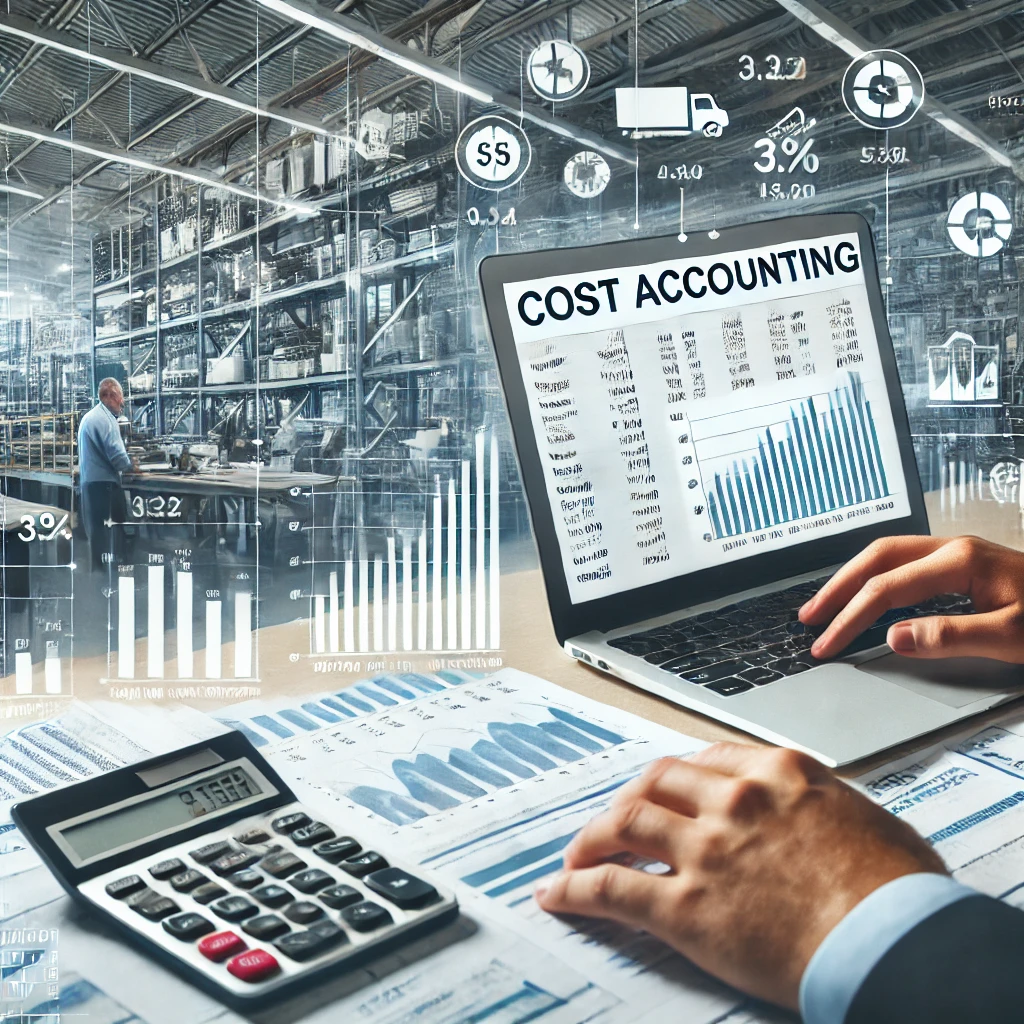
Understanding Cost Accounting: A Guide for Manufacturers
Cost accounting helps manufacturers control costs, optimize pricing, and improve profitability by detailing production expenses. Automated tools like Superunit can handle up to 80% of these tasks with 3x the accuracy, letting manufacturers focus on strategic growth while ensuring precise cost tracking and scalability.
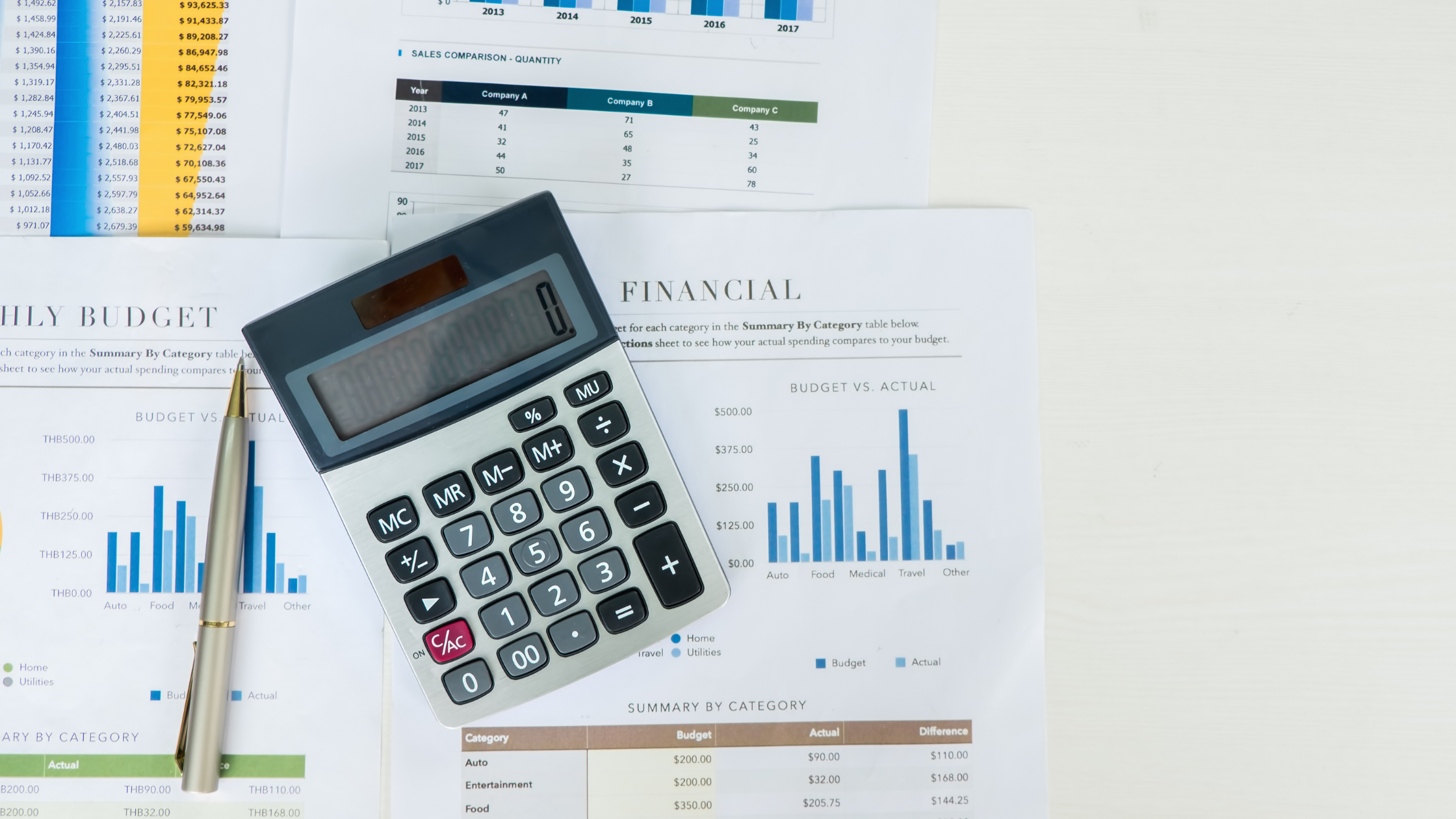
The Essential Guide to Automated COGS Tracking for Inventory Businesses
Accurate COGS tracking is key for inventory businesses' unit economics and profitability. Automate calculations for real-time cost visibility, precise gross margins, time savings. Learn strategies like AI matching, duty allocation, seamless data integration.
%20(1).png)
The Cost of Goods Sold Formula Explained
This comprehensive guide explains the cost of goods formula in detail using real world examples Topic covered include beginning inventory, purchases, ending inventory, and how these elements interact. Discover the significance of this formula in financial reporting, inventory valuation, and overall business decision-making.
Ready to get started?
Take control of your accounting and inventory management today. Say no to spreadsheet hell and uncertainty.